Current strikes showcase the need to future-proof North America’s supply chain.
What we know, and what we can do right now.
What we know, and what we can do right now.
The East Coast port strike may be the latest, but it won’t be the last. What can we learn from recent events, and what can occupiers do now to mitigate future supply chain disruption risks?
First things first: what’s happening right now in Montreal and across East Coast ports in the United States?
The Montreal (Canada) and U.S. East Coast port strikes may be the latest, but they won’t be the last. This effectively put a stop on 40% of the port’s container traffic as the local union works to hammer out a deal with the Maritime Employers Association (MEA). Contracts between the two expired in December and they have been unable to come to agreeable terms for continued engagement thus far.
And Tuesday, longshore workers walked off the job in a similar fashion in the United States, setting into motion a long-anticipated strike across all Atlantic and Gulf Coast ports, while the United States Maritime Alliance (USMX) and International Longshoremen’s Association (ILA) work out labour agreements.
And Tuesday, longshore workers walked off the job in a similar fashion in the United States, setting into motion a long-anticipated strike across all Atlantic and Gulf Coast ports, while the United States Maritime Alliance (USMX) and International Longshoremen’s Association (ILA) work out labour agreements.
The strike effectively puts a halt on the flow of a wide variety of goods coming into the States: everything from bananas and clothing to household goods and auto parts and, notably, critical parts needed to keep US factories (and plant jobs) running, while the United States Maritime Alliance (USMX) and International Longshoremen’s Association (ILA) work on an agreement.
Before strike | Port Newark Container Terminal - Newark, NJ
After strike | Port Newark Container Terminal - Newark, NJ
Source: PNCT
Ports impacted by Montreal and East Coast strikes
Disputes like these are all too familiar these days, as supply chain disruptions in places like the United States, Canada, China, Egypt, Panama, and many more critical locations, seem to be occurring a few times each year now—with the last major North American strike having taken place only a little more than a month ago across Canadian rail systems.
What happened during the recent Canadian rail strikes?
Union labour disputes with the Canadian National Railway Company (CN) and Canadian Pacific Kansas City (CPKC) led to a mass freight railway shutdown in August.
While the strike—from lockout to ordering trains to resume operations—lasted only a day, its impacts extended wide across the supply chain (imports and exports), had U.S. trade implications, and impacted commuter train functionality for tens of thousands of people, creating myriad ripple effects.
While the strike—from lockout to ordering trains to resume operations—lasted only a day, its impacts extended wide across the supply chain (imports and exports), had U.S. trade implications, and impacted commuter train functionality for tens of thousands of people, creating myriad ripple effects.
In a similar fashion, this week’s port strikes could lead to shipping backlogs five times the length of halts, with a variety of major impacts felt across retail, automotive, energy, manufacturing, and agricultural sectors.
What can the rail strike tell us about what might happen next during the port strikes?
We can look at what happened during the recent Canadian rail strike and past port strikes for indications of what might come next for the U.S. and Canada with the port strikes now in full swing.
Shuttered ports could delay U.S. coal exports to Europe, for example, impacting heating and energy shortages across the Atlantic. The U.S. auto industry could also be hit particularly hard, with anticipated delays in imported and exported vehicle component parts. And a wide variety of household goods we use daily could become in demand quickly as bottlenecks and delays increase need—and prices—for both countries.
The majority of U.S. agricultural exports are shipped from East/Gulf Coast Ports. More than 30% of 2023 exported crop was containerized. With the heart of harvest season in North America lasting between October and November, perishable, time-sensitive goods are on the line.
Shuttered ports could delay U.S. coal exports to Europe, for example, impacting heating and energy shortages across the Atlantic. The U.S. auto industry could also be hit particularly hard, with anticipated delays in imported and exported vehicle component parts. And a wide variety of household goods we use daily could become in demand quickly as bottlenecks and delays increase need—and prices—for both countries.
The majority of U.S. agricultural exports are shipped from East/Gulf Coast Ports. More than 30% of 2023 exported crop was containerized. With the heart of harvest season in North America lasting between October and November, perishable, time-sensitive goods are on the line.
A prolonged strike could cripple the agricultural export market share, and surge prices for consumers, while dropping prices for producers. A strike would cause disruption, and likely increase prices on consumer staple foods that are also being imported, largely via container, such as bananas, other fruits, vegetables, and other grocery items at a time when inflation is one of the largest issues out there.
According to JP Morgan and Reuters, the estimated economic impact of the shutdown in the U.S. could be as high as $5 billion (USD) or more. The 13-day dockworker strike in British Columbia last year was estimated to have cost the economy $250 million (CAD) per week.
Both strikes also come with risk of leaving shippers stranded at sea, anchored until further notice, with myriad untold impacts. And with billions in goods crossing the U.S.-Canada border each day, helping both economies, it’s easy to say that there’s a lot at stake, even if the ports shutter for a day, let alone days to weeks at a time.
According to JP Morgan and Reuters, the estimated economic impact of the shutdown in the U.S. could be as high as $5 billion (USD) or more. The 13-day dockworker strike in British Columbia last year was estimated to have cost the economy $250 million (CAD) per week.
Both strikes also come with risk of leaving shippers stranded at sea, anchored until further notice, with myriad untold impacts. And with billions in goods crossing the U.S.-Canada border each day, helping both economies, it’s easy to say that there’s a lot at stake, even if the ports shutter for a day, let alone days to weeks at a time.
Are there any external factors that could also play a big role in port strike negotiations?
While the Montreal strike is currently set to a three-day timeframe, impacts of Hurricane Helene’s recent path of destruction and the upcoming U.S. presidential election will be on opposite ends of the line in the U.S., in a negotiation that has no set timetable.
While some may try to come to a quicker conclusion to avoid stalling critical aid, others may hold out for fear of what foreign policies may soon be on the horizon. What is clear is that much will be on minds right now as short- and long-term ramifications are pit against worker needs and desires.
While some may try to come to a quicker conclusion to avoid stalling critical aid, others may hold out for fear of what foreign policies may soon be on the horizon. What is clear is that much will be on minds right now as short- and long-term ramifications are pit against worker needs and desires.
A resolution to the strike is layered with complexities during a presidential election year. It is uncertain what steps will be taken to get the ports up and running again and how quickly a resolution will be reached.
The good news? At least in the U.S., we did see this coming.
While ports didn’t receive much beyond short notice in Montreal, U.S. ports have been planning this for some time, allowing for interested parties to act accordingly. In anticipation of a potential strike or stoppage in the U.S., shippers began sending more container volume to the West instead of the East Coast earlier this year, with Los Angeles seeing a peak month of delivery in June. Peak seasons also moved up about six weeks across the board, with a potential slower than usual fourth quarter as shippers work through impacts.
Another plus? Safety stock and restock has continued to be a popular post-pandemic strategy. Many companies have more warehouse space now to build and maintain inventory levels to weather all seasons, including many retailers whose pre-purchased supply ahead of a Q3/Q4 holiday shopping season could be sufficient to sustain across many lines of goods. So, when, as of Sunday, the Port of New York – New Jersey began halting the acceptance and processing of export cargo unless it could be loaded prior to Monday, some were ready for it.
For those less prepared, what should occupiers across North America do now to mitigate current and future risk during events like this?
Supply chains have never been more fragile amidst shifts in global production and consumption. Consumers are increasingly invested in convenient retail (direct to doorstep) at a time when the labour movement is only growing in power.
While increased production in Mexico and recent railroad mergers across the North American transportation network have left us more connected than ever before, this concentration also carries risk.
Luckily, there is a lot occupiers in this space can do right now to make it through tough times in the future:
While increased production in Mexico and recent railroad mergers across the North American transportation network have left us more connected than ever before, this concentration also carries risk.
Luckily, there is a lot occupiers in this space can do right now to make it through tough times in the future:
- Add on. More warehouses or short-term space for season overflow in more places helps spread out risk.
- Bring operations closer to home. Shifting production closer to consumption means less distance to travel, less delay when delays occur.
- Diversify hubs. Spreading out ports, including a mix of U.S. and Canadian ports, can help ensure that, no matter what, operations don’t come to a full halt.
- Engage outside. Utilize a 3PL to help handle ebbs and flows in demand, have drayage drivers on standby, and be able to quickly arrange for alternative shipping methods.
- Have a plan for extra. Determine the best lease/sub-lease plan for proactive excess inventory, and be ready with extra parking for containers or for large amounts of products (from delay or otherwise) that might come in all at once.
With tactics like these in place, the industry may be better prepared to keep things running and ready, regardless of when the inevitable next big disruptor hits.
Subscribe to receive national industrial market reports and insights
Article contributors
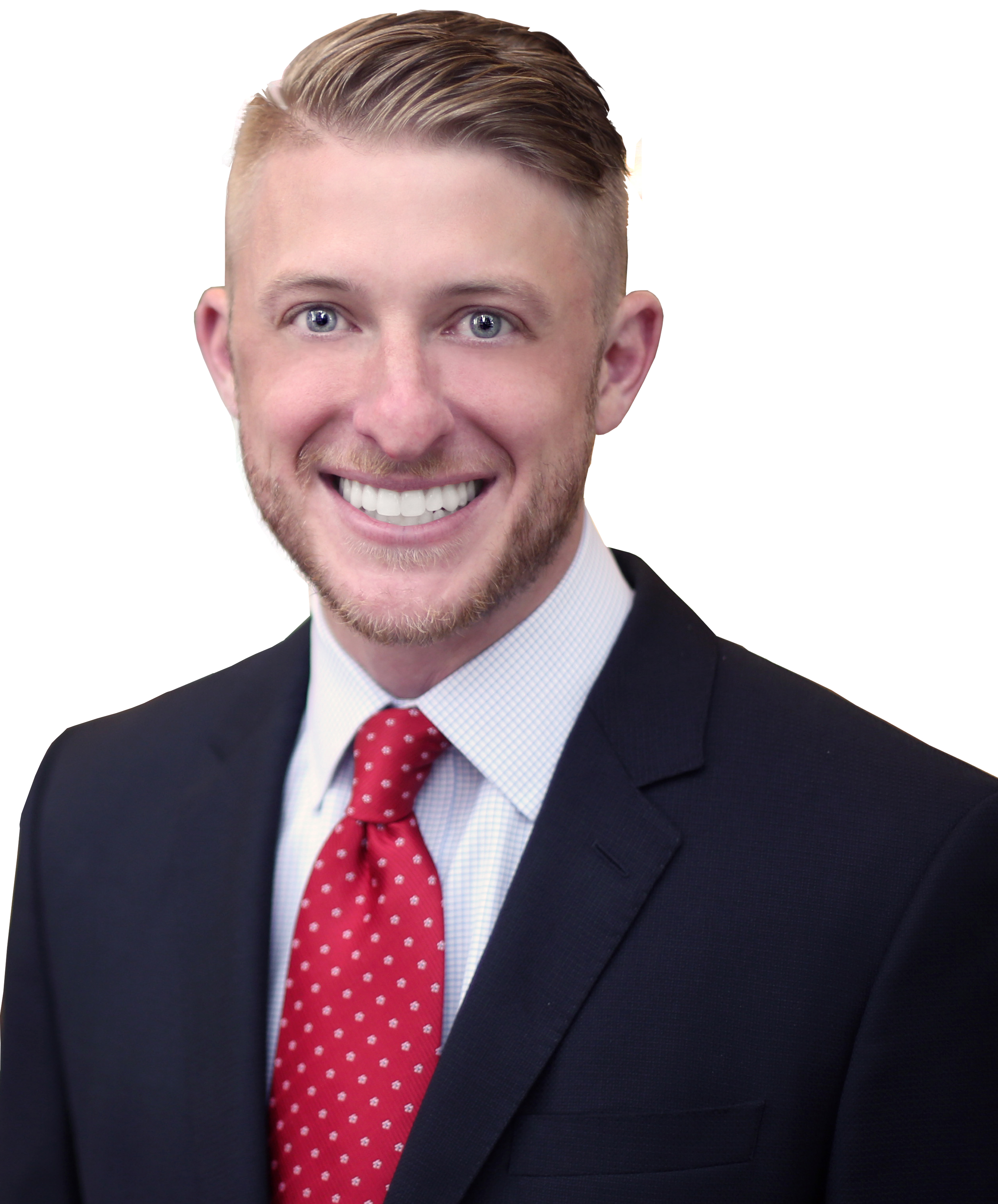
-
Director
-
Industrial / Supply Chain & Logistics Market Intelligence
-
Research Manager
-
Toronto Suburban Markets
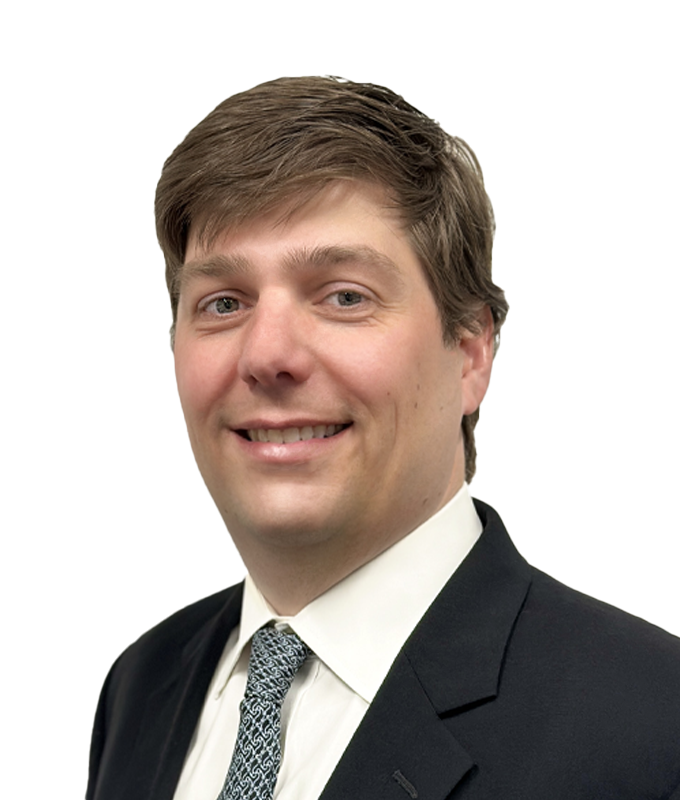
-
Manager, Market Intelligence
-
Industrial Logistics Market Intelligence